Wheels that make the world go round....
Over the last two years the world has discovered the complexities of the Supply Chain. Hit by a multitude of shortages, challenges, and unprecedented demand, one running theme within the U.S. has been around the shortage of chassis. For those that are unfamiliar with intermodal logistics, in the container world a chassis is needed to move any form of container, as containers themselves do not have a set of wheels or means by which to be pulled. Without a set of wheels, the steel box hauling your freight isn’t going to get very far!
The chassis shortage has had an impact on par with some of the more newsworthy items like the tight labor market, shipping container shortages, and congested ports.
What caused the shortage?
As quickly as the U.S. began to climb out from the initial stages of the pandemic, freight demand began to skyrocket. It became clear that with this surging demand and a general imbalance of import vs. export that the supply of equipment for freight movements would be taxed beyond what it could keep up with. While container shortages were driven more globally, the U.S. market experienced some specific challenges around its chassis infrastructure that we are still struggling to recover from.
While consumer habits and demand are the obvious drivers in the utilization of chassis, two factors have continued to keep the chassis shortage as a persistent issue: excessive dwell times and a shutoff of new manufacturing supply from China.
The majority of intermodal equipment manufacturing currently takes place in China. This supply was hampered significantly following the anti-dumping sanctions levied earlier this year against the largest Chinese chassis manufacturer. Effectively 85% of available chassis manufacturing is no longer allowed to be shipped to the U.S., and domestic manufacturers have not been able to scale quickly enough to meet the demand and needs of the U.S. network. This ultimately means there has been minimal relief and progress on inventory recovery.
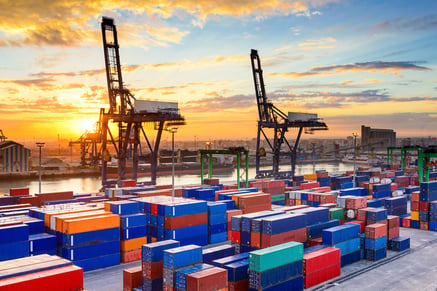
“Many shippers have begun shifting imports to come through East Coast or Gulf ports to avoid delays in Long Beach and L.A. This is creating unanticipated demand pressure on equipment in markets that would typically not be importing as heavily as they are right now. This ultimately impairs units from being repositioned into other markets,” explained Intermodal expert and Radiant Road & Rail Senior Vice President, Christopher Brach. “Steamship lines and equipment owners are seeing significant increases in unit dwell time while equipment is in a customer’s possession. From several providers there have been trends of containers & chassis average use hovering around 45% longer than would be traditionally experienced. While customers may feel they are safeguarding their use of the equipment, this is inefficient and has impacted the ability to plan and meet demand as chassis owners are unable to predict unit availability.”
How long is this projected to last?
General consensus is that this shortage will last into 2023. It could take several months before there are enough chassis available to handle the surge of import containers congesting U.S. ports and inland rail ramps. New capacity is coming, but it is coming online slowly due to the sanctions and production capabilities. As new units continue to roll out, we should see a slow improvement as time goes on.
What are your options?
Customers should look to turn their units rather than sitting on them. Minimizing dwell on units and balancing inbound/outbound capacity for optimal chassis utilization will be vital to generating chassis availability. Being aware of this turnaround time can lessen the strain on others.
Be sure to talk to a Road & Rail expert about your freight forwarding options. As part of the Radiant network, we can leverage the collective capacity along with key relationships to ensure that your shipments get where they need to go, when they need to get there.